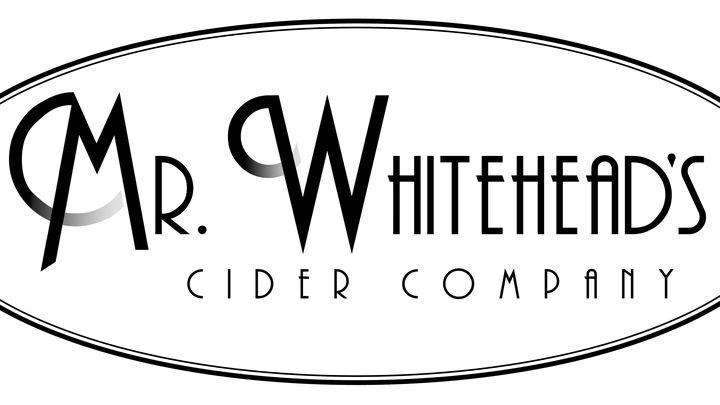
Relocation assistance
Donation protected
Hi, my name is Angus and I have been making cider, apple juice and cider vinegar in Hampshire for 20 years. As you are no doubt aware, unfortunately, we have to move out of our premises at Windmill Farm, where we have been for the last 12 years. This was not our choice to do so, but the owner of the building requires it back to expand his own business.
As many of you probably know, the 2022 apple harvest was the best that we (and most of you) have had in many a long year…!
The benefit of this is that we have a very large amount of stock (liquid assets!), but the downside is that we have had to move it all – which has turned out to be around 400,000 litres of cider and vinegar!
Whilst having such a good harvest was very much something to celebrate, it has also been somewhat logistically challenging to move it all to our new site…
to the extent that we had to empty one tank into a lorry tanker….. then move the tank…… then move the liquid…… then refill the tank…… then empty the next tank into the lorry tanker…… then move it….. and so on….!
As you can appreciate this has not been a five-minute job to do. In fact, we were still pressing apples upto the last day of November, and from the 1st of December we have been steadily moving everything to the new site. Luckily this is only a couple of miles down the road, but it has still proven to be a very big logistical challenge.
Also, as the new building has started as a basic shell, we’ve needed to run a power and water supply to it and carry out various other jobs and tasks to make it weatherproof and fit for our purpose of pressing apples and making juice, cider and vinegar.
Moving premises in the winter seems a lot harder too, with the short, cold and often wet days – lots of mud to deal with! Certainly not the ideal time to do it, but there was no other option.
We are now getting towards the final stages of moving everything FROM the original site, but sadly we are still quite a long way from being up and running at the new site. Suffice to say, we are in a rather awkward situation now.
Although I have been planning this for the past year now, things don’t always run smoothly, or happen in the right order. A lot of our equipment is currently being stored outside (which is not ideal for the bottling machinery), and until we are able to finish off some structural work inside the new building, we are struggling to progress. However, we have still been required to get all of our stock and equipment out, and this is now being stored in various different locations.
The upshot of all this is, that we could do with a little bit of help if possible.
For example, we can’t move the apple pressing machine into the new building until we have levelled and laid the floor for it, and hired a forklift capable of lifting 10 tonnes. We can’t install the bottling machinery until we have installed the electrical system inside the building. And we can’t switch our vinegar machine back on until we can pay for a crane to remove it, transport and reinstall it at the new site.
Sadly if we can’t get through the next 3 weeks, I fear we won’t be able to press any apples at all this coming autumn, and could also, therefore, lose a lot of business (I have already had to turn down some good new juice and cider making contracts because of the amount of time that has been tied up with the move) – meaning a struggle to survive. We are still trading and selling stock, but much of my time is currently spent dealing with the move, and not concentrating on sales and production.
Therefore, I am asking if there is any chance of some help. This is mainly to keep the move underway, and to do some preparation in the new building – so primarily financial help to:
• Paying for a specific invoice (e.g. the day hire of a lorry), hire of a crane to move tanks / machines etc.
• Allowing us some dry storage to put the bottling machinery in, until either it will be re-installed, or the surplus kit can be sold – It is far from ideal being stored outside in the wet.
• Help with the purchase of some concrete / concrete railway sleepers to strengthen the floor, and costs of the associated groundworks.
Although having just under a year’s notice may sound like a long time, when you think of the size of our operation, there is a lot to cram into that time period- especially when this includes finding a suitable site in the first place, then designing the layout of the building so that it can suit the nature of our business etc. Plus including 4 months of solid apple pressing in the middle of it all…!
I’ve run this business for 20 years now, and have seen it go through a lot of changes – we have diversified at every step of the way, every turn – from simple cider making to sell at Farmers’ Markets and local pubs, through to supplying local schools with apple juice, and now cider vinegar production – which has been a real lifeline to us in the last couple of years - I have picked up over a dozen significant customers in the past 18 months, ranging from one that takes 5000 litres per year to one that takes over 100,000 litres.
I hope that you agree we have provided a good service over the years, and that bringing us your apples in exchange for juice / cider / vinegar etc has been a positive thing, has helped us all collectively reduce waste (and been quite a fun thing to do too!).
I’m dedicated to continuing to do this, and to carry on providing such a service to you (and hopefully many more people in the future too)…
Thanks and best regards,
Angus Whitehead
Director
Mr. Whitehead’s Cider Company Ltd.
Co-organizers (2)
Angus Whitehead
Organizer
Laura Hilson Pater
Co-organizer